 |
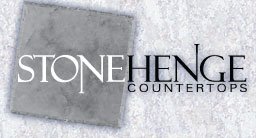 |
 |
 |
Glossary of Terms Used with Concrete Countertops
click on the letter to explore the countertop glossary.
A
- Accelerated Curing – the intentional addition of heat to the concrete environment to accelerate the rate at which the concrete achieves the desired hardness for demoulding.
- Admixture – material other than cement, water, and aggregates used as an ingredient in a concrete mix to alter properties, such as workability, curing temperature range, set time or color.
- Acrylic Sealer – a simple, single-component polymer that is either water or solvent based. These sealers can allow moisture penetration, scratch more easily than some others, and provide moderate stain protection.
- A-frame – an A-shaped assembly used to transport countertop slabs on edge.
- Apron Front Sink – also known as a farm or farmhouse sink. These sinks have a large apron in front and sit on a short cabinet. The countertop wraps around these sinks on the sides and back edge only not in the front.
B
- Beam – a horizontal structural member capable of withstanding load primarily by resisting bending. By definition, a concrete countertop is a beam because it spans some open spaces between cabinet side panels.
- Bughole – a small void in formed concrete surfaces caused by an entrapped air bubble. The use of a vibrating table and selected admixtures can significantly reduce the appearance of bug holes in the surface of a poured concrete top.
C
- Cantilever – a beam that projects beyond its supports. In the case of a countertop, any place where it overhangs a cabinet or support by more than a few inches.
- Caulk – an ideal material for filling seams between countertop slabs. Typically made of a flexible material such as acrylic, the caulk creates a control joint between two slabs that helps prevent problems due to expansion and contraction.
- Cement – fist used by the Romans, cement is the principal bonding agent used in producing concrete. See CSA Cement and Portland cement below for more specifics.
- Cenospheres – hollow lightweight spheres filled with air or gas, typically produced as a byproduct of coal combustion at power plants (see microspheres).
- Coarse Aggregate – particles generally ranging between 3/8 and 1 ½ inches in diameter that are included in a concrete mix design. We use 3/8 Delaware River pea gravel in a mix of browns, tans, and reds as our primary course aggregate.
- Compressive Strength – the ability of concrete to resist compression forces, or pushing together forces, expressed in pounds per square inch (psi). Our mix designs are specially formulated to produce concrete high compressive strengths.
- Concrete – created by mixing cement, water, and aggregates like sand and gravel together to form a hard long lasting form.
- Concrete Countertop – a handcrafted alternative to the other mass manufactured countertop surfaces.
- CSA (Calcium Sulfoaluminate) Cement – a newer type of cement that hardens very rapidly. The advantage of using CSA cement over Portland is that it can achieve compressive strengths exceeding 5000 psi in one day versus 28 days for conventional cement.
- Curing – the maintenance of moisture and temperature within freshly poured concrete during a defined period following casting to assure adequate hydration of the cementitious materials and proper hardening of the concrete.
D
- Drain Board – pitched grooves or a depressed area in a countertop next to an undermount sink that allows water to run into the sink.
- Drop-in Sink – a sink that has a rim that fits over the countertop. These sinks are known as self-rimming or top-mount.
E
- Edge Return – a countertop edge that is thicker than the rest of the slab, to give the appearance of a thicker slab.
- Engineered Stone a man-made countertop also called quartz. Engineered stone slabs are made from approximately 93% crushed quartz that is rebounded with resins, pigments, and binders. These countertops give a visual impression similar to granite, but are more consistent in their patterns and have no natural veining.
- Epoxy Sealer – a dual component system that reacts when mixed to form a hard, durable surface over the concrete. Epoxy sealers are excellent for high gloss surfaces and provide the depth of a candy apple finish.
F
- Fibers – tiny filaments added to a concrete mix to control shrinkage cracking during the cure cycle. Unlike rebar, fibers do not provide structural reinforcement. Some of our mix formulas include polyvinyl alcohol (PVA) glass fibers.
- Film Forming Sealer – a type of sealer that forms a surface film to block the penetration of water and contaminants. Film forming sealers are available in various gloss levels ranging from dull on up to gloss and typically enhance the color intensity of the finished concrete surface.
- Fine Aggregate sand used in a concrete mix (also known as fines).
G
- GFRC (Glass Fiber Reinforced Concrete) – in use for over 30 years to produce many concrete products, especially thin architectural cladding panels. Using glass fibers in a concrete mix allows a fabricator to pour a thinner slab that matches the strength of a conventional slab twice its thickness. Since less material is needed for the same strength, GFRC uses less Portland cement than regular concrete, and is greener as a result.
- Grinding – a mechanical surface preparation method produced with abrasive discs that abrade the surface for smoothing or to reveal course aggregates below the original surface.
I
- Install – to set a countertop onto cabinets and caulk any seams so that the countertop fits well, is level, adjacent slabs are flush, and fixtures such as sinks are properly mounted.
- Integral Sink – a sink casted as part of the concrete countertop. Concrete is the only countertop material (other than solid surface) where a sink of the same material can be formed as part of a top.
K
- Knockout – a rubber or shape placed in the form where a faucet hole in the countertop is needed.
M
- Melamine – melamine panels provide an ideal material for making molds to cast concrete countertops because of its smoothness and easy release.
- Metakaolin – a pozzolan admixture for concrete that replaces 10% - 20% of the Portland cement used in the mix design.
- Microspheres – very fine, lightweight hollow ceramic spheres that are chemically identical to fly ash but too large to produce pozzolanic reactivity. These can be used to replace some of the sand for lightweight concrete or to modify the consistency of the concrete to make it stiffer and less sticky.
- Mortar Mixer – a mechanical mixer that uses rotating paddles attached to a horizontal axle to blend the mix ingredients of mortar or concrete. We use a mortar mixer for mixing concrete needed for our countertops.
P
- Penetrating Sealer – a sealer that penetrates into the concrete surface to increase water repellency and resist stains. Penetrating sealers are used by some concrete countertop fabricators who want to create a natural concrete look. These sealers do not offer as durable protection as a film based sealer.
- Pigment – a finely ground natural or synthetic particle that adds color and opacity to a concrete mix, topping, or stain.
- Plastic Shrinkage Cracks – irregular cracks that may occur in fresh concrete if there is a rapid loss of water on the surface before it has set. Most of our tops are poured inverted, so the top surface is against the mold and not exposed to air while curing. These cracks are not structural.
- Primary Reinforcement – structural reinforcement designed to carry tension forces in reinforced concrete. Rebar, ladder wire and structural carbon fiber grid are all primary reinforcement materials and each has different applications and characteristics.
- Portland Cement – generally available in three types:
- Type I is the general purpose cement. Available in ordinary grey and white, sets up in approx. 16 hours and reaches full cure in 28 days.
- Type II cement – sulfite-resistant cement, used where the product may be affected by ground water.
- Type III cement – a high-early strength cement that provides high strengths in usually a week or less, yielding 28 day strengths in 7 days. This is also known as high-early cement.
- Pozzolan – a material exhibiting cementitious properties when combined with calcium hydroxide. Pozzolans are included in a mix design to replace some of the Portland cement needed. Using less Portland has positive environmental benefits; as an added bonus, many pozzolans in use today are recycled materials derived from post-industrial waste products like fly ash and blast furnace slag that were previously sent to landfills.
R
- Rebar – short for reinforcing bar. Rebar may be cast into a countertop to increase its tensile load bearing ability, particularly important in cases where a top is cantilevered. Rebar is ribbed steel bars sized by eighths of an inch of the bars diameter; our countertop rebar is a 3/8 diameter size. With the addition of rebar, our concrete tops are transformed into a strong, ductile material.
S
- Sealer – sealing the top is the final fabricating step because an untreated concrete countertop is porous and will absorb water and stains. Fabricators typically use either a solvent based penetrating sealer or a film forming sealer. A good sealer will block the penetration of oils, chemicals, and stains, and make the concrete surface easier to clean and maintain. (See film forming sealer and penetrating sealer for more information.)
- Seam – a joint between 2 adjacent pieces of countertop material. Seams are used in cases where a single piece would be too large to transport and place into position. Concrete countertop seams are typically silicone caulked or grouted.
- Secondary Reinforcement – non-structural reinforcement materials usually employed to control shrinkage cracking. These include scrim, carbon fiber webbing, or PVA or fiberglass fibers.
- Shim – a tapered piece used during installation to level adjacent countertop slabs. Shims may also be used to provide support to tops when the cabinets are not level.
- Shrinkage – concrete naturally shrinks as it cures. We used admixtures in our mix design to limit the water needed to minimize this tendency.
- Slurry – a cement paste used to fill bugholes in countertops.
- Shrinkage Reducing Admixture (SRA) – used to break down the surface tension of mix water and prevent capillary water from pulling on the concrete as the water evaporates.
- Stamped Concrete – the impressing of a patterns and/or textures onto the surface with flexible mats before it is fully dry. We use this technique to create countertops that replicate natural stone and slate.
- Stain – concrete's porous qualities and neutral tone makes it the perfect canvas for topically applied color. There are several types of concrete stains.
- Acid-Based: chemically react with the concrete surface and can produce a beautiful variegated look. These reactive stains are in a water based acidic solution which includes metallic salts that cause a reaction with the lime content in concrete. When the reaction occurs, the stain forms a permanent bond with the concrete.
- Dye-Based: these stains can be suspended in solvents or water. Dyes are generally composed of fine acrylic pigments mixed with a quick drying solvent like alcohol.
- Water-Based: these are nonreactive stains commonly with an acrylic binder. These stains work by penetrating the surface of the concrete to deposit the pigments inside of the open pores. The choices of color are much broader in this class of stains than any other.
- Super Plasticizer (aka Super P) – an admixture that produces a cement that flows easily with lower water content than would be needed otherwise. Superplasticizers are technically high-range water reducers (HRWR) that make a mix more fluid without substantially delaying the set time or increasing air entrainment. Mixes that use less water produce stronger concrete.
T
- Tensile Strength – the ability of concrete to resist tension forces, or pulling apart forces, expressed in pounds per square inch (psi).
- Template – a physical pattern made on top of installed cabinets to represent the proper size of the finished countertop. Templates are then taken back to the shop and used to properly size the molds for a precast concrete countertop.
U
- Undermount Sink – a sink that is mounted underneath the countertop with a finished cutout.
- Urethane – a type of sealer that is tougher and more scratch-resistant than acrylics. Urethane sealers provide good stain, heat and scratch resistance but do not offer the same UV stability.
V
- VCAS (Vitreous Calcium Alumino-Silicate) – a supplementary cementitious material with pozzolanic properties, derived from post-industrial glass fiber waste. We use VCAS to replace some of the cement in all our Portland based mix designs.
- Vessel Sink – a sink that sits on top of the countertop.
- Vibration Table – helps distribute wet concrete evenly in the mold and to reduce the problems of bug holes from entrained air bubbles.
W
- Water Reducer – an admixture that either increases the slump of freshly mixed concrete with lower water content or maintains workability without affecting the strength.
- Wax – applied to concrete countertops has a nice feel, but is marginally effective as it provides a small degree of protection against stains but wears away quickly and must be reapplied often.
- Wet Polishing – a method for smoothing concrete that uses water to cool the diamond abrasives and eliminate grinding dust.
- White Cement – a Portland cement with a low iron content that hydrates to a white paste. This cement is ideally used for integrally colored concrete where bright color tones, especially pastels, are desired.
|
 |
 |